Revolutionizing Automotive Manufacturing: Top Trends and Techniques
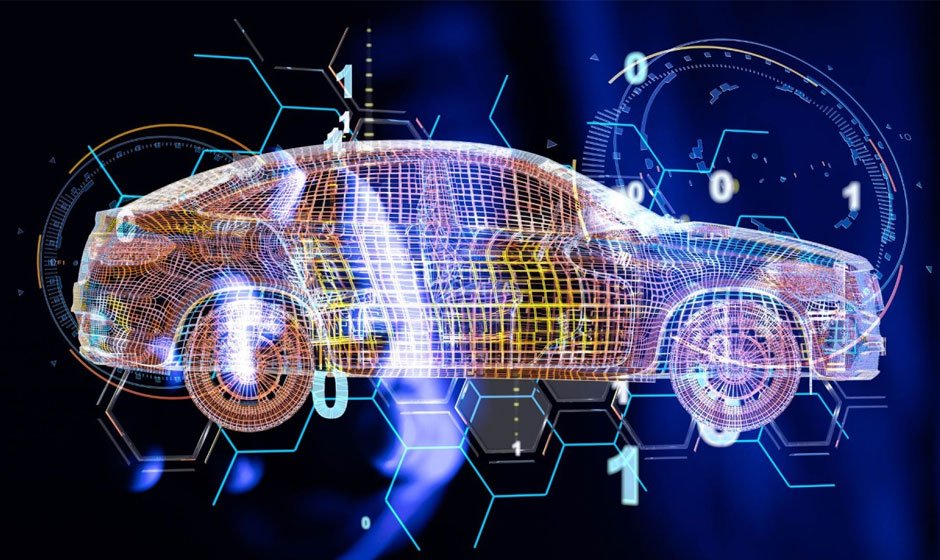
The intricate dance of automotive manufacturing has evolved from rudimentary assembly lines to state-of-the-art, automated factories empowered by Industry 4.0. The manufacturing processes that once took days are now accomplished in a matter of hours or even minutes, thanks to advancements in technology and the integration of digital techniques.
In this article, we will explore the top trends revolutionizing automotive manufacturing, looking closely at how these innovations promise to redefine the industry’s future.
Shift toward Electric Vehicle (EV) Manufacturing
One of the most significant trends reshaping the automotive manufacturing landscape is the rapid shift toward electric vehicles. With the increasing awareness of the environmental impact of conventional internal combustion engine vehicles, consumers and governments alike have turned their attention to electric alternatives. This surge in demand has driven automakers to invest heavily in EV manufacturing.
EVs present unique challenges and requirements compared to traditional vehicles. Key components such as batteries, electric motors, and power electronics demand specialized manufacturing processes. Battery technology, in particular, plays a pivotal role in the performance and range of EVs. As a result, automotive manufacturers are investing in cutting-edge battery assembly lines that can efficiently produce high-quality batteries at scale.
Advancements in Automation and Robotics
Automation and robotics have been a staple in automotive manufacturing for decades. However, recent advancements in these fields have brought about transformative changes in assembly lines. Traditional robotic arms have given way to more sophisticated and versatile machines that can handle complex tasks with precision and speed.
Collaborative robots, or cobots, are one of the significant breakthroughs in automotive manufacturing. Unlike their industrial counterparts, cobots are designed to work alongside human operators, promoting safer working environments and increased flexibility on the production floor. They can perform tasks that are too delicate or intricate for traditional robots, allowing for seamless human-machine collaboration.
Artificial Intelligence (AI) and Machine Learning have also found their way into automotive manufacturing. AI-powered systems can optimize production processes by analyzing vast amounts of data in real time. They can predict potential issues, identify areas for improvement, and streamline operations for enhanced efficiency and reduced downtime.
Additive Manufacturing (3D Printing) in Automotive Production
Additive manufacturing, commonly known as 3D printing, has revolutionized the prototyping and tooling processes in the automotive industry. Traditional manufacturing methods for prototypes and tooling were time-consuming and expensive. With 3D printing serivce, automotive designers and engineers can quickly produce prototypes, allowing for faster iterations and improved designs.
Furthermore, 3D printing has enabled automotive manufacturers to explore low-volume production and spare parts manufacturing more economically. Instead of maintaining vast inventories of spare parts, manufacturers can 3D print components on demand, reducing costs and wastage.
Additive manufacturing offers several advantages in the automotive sector, including design flexibility, lightweight components, and the ability to create complex geometries. However, challenges such as material limitations, production speed, and scalability need to be addressed to fully capitalize on its potential.
Integration of the Internet of Things (IoT) in Smart Manufacturing
The Internet of Things (IoT) has emerged as a game-changer in the automotive manufacturing process. IoT-enabled sensors are integrated into various stages of production, allowing manufacturers to gather real-time data on machine performance, production rates, and product quality. This data-driven approach enables better decision-making and process optimization.
One of the significant applications of IoT in smart manufacturing is predictive maintenance. By continuously monitoring machinery and equipment, manufacturers can detect potential issues before they lead to costly breakdowns. Predictive maintenance not only reduces downtime but also extends the lifespan of manufacturing equipment.
Moreover, IoT enables seamless communication and coordination between different stages of the production process. This interconnectedness enhances supply chain management, production scheduling, and quality control, resulting in improved overall efficiency.
Conclusion
The automotive manufacturing industry is going through a significant transformation due to the rise of electric vehicles, automation, additive manufacturing, and the Internet of Things. Electric vehicles are reshaping production processes, and automation, robotics, AI, and machine learning are improving productivity and safety.
Additive manufacturing has revolutionized prototyping and production, reducing costs and lead times. Integration of IoT enables data-driven decisions and real-time monitoring. To stay competitive, manufacturers must adapt to these innovations, fostering growth, profitability, and sustainability in the industry. A new machining revolution is underway.