Sheet Metal Prototyping: A Powerhouse in the Food Processing Industry

The food processing industry is a complex and demanding environment, where hygiene, efficiency, and durability are paramount. Sheet metal prototyping has emerged as a powerful tool in this industry, offering a versatile and cost-effective solution for creating prototypes of critical equipment and components. This article will delve into the world of sheet metal prototyping in the food processing industry, exploring its significance, applications, hygiene standards, compliance considerations, and durability factors.
Importance of Sheet Metal in the Food Processing Industry
Sheet metal prototyping, with its unique combination of strength, formability, and resistance to corrosion, plays a crucial role in the food processing industry. It offers numerous advantages over other materials, including:
- Durability: Sheet metal components can withstand the harsh conditions of the food processing environment, including high temperatures, moisture, and chemical exposure.
- Hygiene: Stainless steel, a common type of sheet metal, is highly resistant to bacteria and easy to clean and sanitize, ensuring food safety.
- Versatility: Sheet metal can be easily formed into complex shapes, making it ideal for creating a wide range of equipment and components.
- Cost-effectiveness: Compared to other materials, sheet metal prototyping is often a more affordable option, particularly for initial prototypes and small-scale production.
These advantages make sheet metal a popular choice for various applications in the food processing industry.
Applications of Sheet Metal in Food Processing
Sheet metal plays a pivotal role in various applications within the food processing industry. From fabricating processing machinery to manufacturing conveyor systems, sheet metal ensures the production of durable and compliant equipment, emphasizing efficiency, hygiene, and compliance with industry standards.
Equipment Fabrication
Equipment fabrication is a crucial aspect of sheet metal applications in the food processing industry. Sheet metal is used extensively in fabricating various equipment used throughout the food processing cycle, including:
Processing Machinery
Processing machinery in the food industry relies on sheet metal for fabrication, ensuring durability and compliance with hygiene standards. Sheet metal’s versatility contributes to efficient and reliable equipment essential for food processing.
- Mixers: Sheet metal is used for the housings, blades, and other components of mixers.
- Conveyors: Sheet metal is ideal for forming the frames and channels of conveyor systems.
- Grinders and slicers: Sheet metal is used for the housings and blades of grinding and slicing machines.
Packaging Equipment
Sheet metal is integral in crafting robust and hygienic packaging equipment for the food industry. Its versatility and durability play a vital role in ensuring compliance with hygiene standards and efficient packaging processes.
- Filling machines: Sheet metal is used for the frames, filling nozzles, and other components of filling machines.
- Sealing machines: Sheet metal is used for the housings and heating elements of sealing machines.
- Labeling machines: Sheet metal is used for the frames and mechanisms of labeling machines.
Component Manufacturing
Sheet metal is fundamental in component manufacturing for the food processing industry. It enables the creation of durable and compliant parts, such as conveyor systems and storage units, ensuring efficiency and adherence to hygiene standards.
Beyond equipment fabrication, sheet metal also plays a vital role in manufacturing various essential components, including:
Conveyor Systems:
- Frames and channels: Sheet metal provides a robust and lightweight structure for conveyor systems.
- Hoppers and chutes: Sheet metal allows for the creation of smooth surfaces for efficient material flow.
- Guards and covers: Sheet metal protects workers from hazards and prevents contamination.
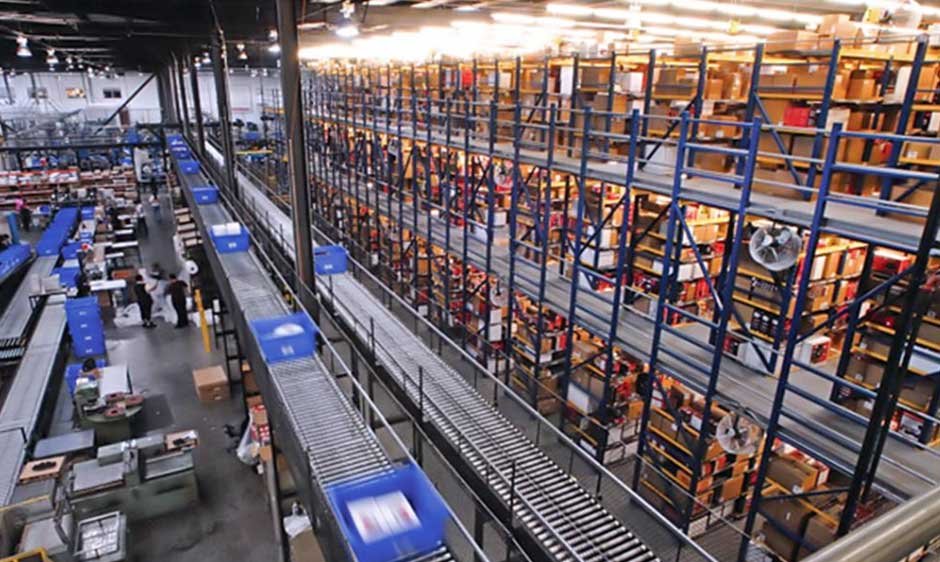
Storage Units
- Tanks and vessels: Sheet metal is used for constructing storage tanks for ingredients, liquids, and finished products.
- Shelving and racks: Sheet metal provides strong and adaptable storage solutions for various food items.
- Bins and containers: Sheet metal is used for creating durable and easy-to-clean containers for handling ingredients and finished products.
Hygiene Standards in Sheet Metal Prototyping
Adhering to stringent hygiene standards is paramount in sheet metal prototyping for the food industry. Compliance with food regulations, easy cleaning, and the selection of suitable materials are crucial aspects ensuring hygienic production processes.
Maintaining hygiene is of paramount importance in the food processing industry. Sheet metal prototyping plays a crucial role in ensuring hygiene through:
Compliance with Food Industry Regulations:
Hygiene standards in sheet metal prototyping for the food industry are upheld through rigorous compliance with regulations, including the FDA’s Good Manufacturing Practices (GMP) and USDA’s Food Safety and Inspection Service (FSIS) standards. This commitment guarantees the safety and hygiene of materials and processes employed in prototype development, aligning with industry regulations to promote food safety and consumer well-being.
Importance of Easy Cleaning and Maintenance:
To enhance hygiene in sheet metal prototyping for the food industry, adopting smooth finishes and eliminating crevices is crucial. This approach minimizes areas where bacteria can accumulate, facilitating easier cleaning and sanitation processes, thereby significantly reducing the risk of contamination in food processing equipment and components.
Materials and Finishes that Meet Hygiene Standards:
In sheet metal prototyping for the food industry, the selection of specific stainless steel types, notably grades 304 and 316, is preferred. Their high chromium content enhances resistance to corrosion and inhibits bacterial growth. Employing polished or electropolished finishes further ensures a smoother surface, facilitating easier cleaning and significantly reducing the risk of contamination in critical food processing applications.
Compliance Considerations
Compliance considerations are pivotal in sheet metal prototyping for the food industry. This involves a comprehensive overview of regulatory standards and requirements, ensuring that the fabricated equipment and components adhere to stringent guidelines set by relevant food industry authorities. This commitment to compliance not only guarantees the safety and quality of the produced items but also establishes trust with regulatory bodies and consumers.
Adhering to food industry regulations is crucial for ensuring the safety and quality of food products. Sheet metal prototyping assists in achieving compliance in several ways:
Overview of Food Industry Regulations and Standards:
In sheet metal prototyping for the food industry, a deep understanding of key regulations, such as the FDA’s Good Manufacturing Practices (GMP) and the USDA’s Food Safety and Inspection Service (FSIS) guidelines, is essential. This knowledge forms the foundation for designing and manufacturing sheet metal components that not only meet stringent hygiene and safety standards but also ensure regulatory compliance. By aligning with these regulations, manufacturers contribute to the overall safety and integrity of food processing equipment and components, fostering a secure and reliable industry landscape.
How Sheet Metal Prototyping Ensures Compliance:
Utilizing food-grade materials, adhering to rigorous cleaning protocols, and thoroughly documenting production processes are integral aspects of achieving compliance with regulatory requirements in the food industry. This comprehensive approach ensures the fabrication of components that meet hygiene and safety standards, fostering transparency and trust with regulatory bodies while emphasizing the commitment to producing high-quality products for the food processing sector
Durability and Longevity
Challenges posed by the demanding processing environment necessitate materials with inherent robustness. Sheet metal addresses these challenges by offering durability, resistance to environmental factors, and a prolonged service life. Examples of enduring sheet metal components in the food industry underscore its reliability, contributing to enhanced efficiency and sustainability in food processing operations.
The food processing environment presents unique challenges to equipment and components. Sheet metal stands up to these challenges due to its inherent properties:
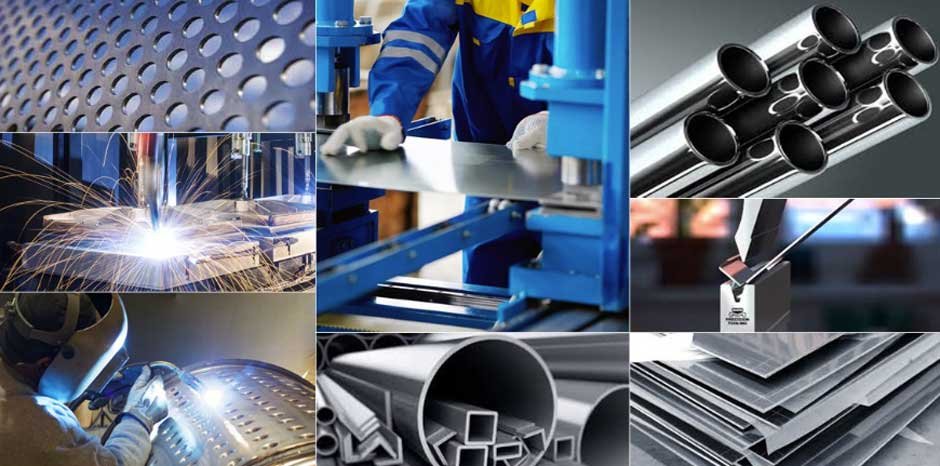
Challenges in the Food Processing Environment:
- Harsh chemicals: Cleaning agents containing acids and alkalis, integral for sanitation, pose a risk of corrosion and degradation to materials in food processing equipment due to their chemical reactivity.
- Extreme temperatures: Food processing frequently entails exposure to high temperatures for cooking and freezing. Such extremes can stress and weaken materials, emphasizing the need for robust and temperature-resistant components.
- Constant wear and tear: The continuous operation and movement of equipment in the food processing industry result in persistent wear and tear, leading to material fatigue. Sheet metal components provide durability to withstand this constant stress.
How Sheet Metal Addresses Durability Requirements:
- Corrosion resistance: Stainless steel grades employed in sheet metal prototyping excel in resisting corrosion from harsh chemicals, ensuring longevity and hygiene in food processing equipment.
- Strength and rigidity: Designed for durability, sheet metal components exhibit strength and rigidity, withstanding the high loads and stresses encountered in the rigorous environment of food processing operations.
- Formability: Sheet metal’s inherent formability allows for the creation of components with complex geometries, enhancing structural strength and rigidity precisely where needed in food processing machinery and equipment.
Examples of Long-lasting Sheet Metal Components in the Food Industry:
- Stainless steel conveyor belts: These belts can withstand years of continuous use and harsh cleaning procedures.
- Shelving and racking systems: Sheet metal shelving and racks offer robust storage solutions for heavy loads of food products.
- Processing machinery components: Sheet metal parts used in mixers, grinders, and other equipment are known for their durability and longevity.
Case Studies
Examining case studies provides tangible evidence of the effectiveness of sheet metal in diverse applications within the food processing industry. These real-world examples showcase successful implementations, highlighting improved efficiency, hygiene, and compliance achieved through sheet metal prototyping.
Successful Applications of Sheet Metal in Food Processing:
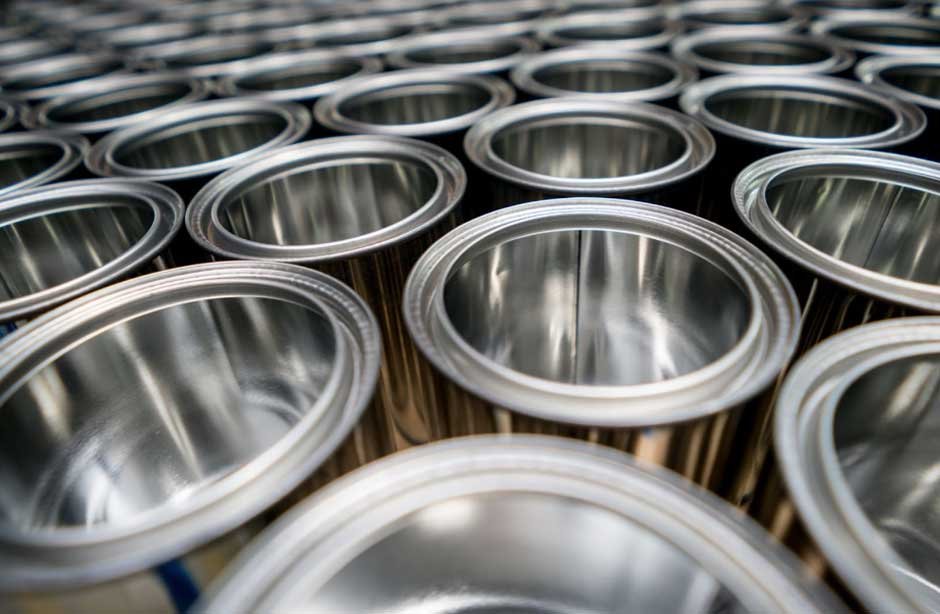
Sheet metal’s successful applications in food processing include fabricating robust machinery, hygienic packaging equipment, and durable components. These solutions ensure efficiency, compliance, and adherence to stringent industry standards.
- A case study of a bakery using sheet metal prototyping to develop a new cookie cutter design, resulting in increased production efficiency and reduced waste.
- A dairy company utilized sheet metal prototyping to create a new design for their milk storage tanks, leading to improved hygiene and reduced maintenance costs.
- A meat processing plant implemented sheet metal prototyping to design custom conveyor systems, optimizing product flow and enhancing worker safety.
Examples of Improved Efficiency and Hygiene Through Sheet Metal Prototyping:
- A beverage company utilized sheet metal prototyping to design a new bottling line, resulting in a 20% increase in production speed and a 30% reduction in water usage.
- A food processing company used sheet metal prototyping to develop a new design for their food handling trays, leading to a significant reduction in bacterial contamination.
- A restaurant chain implemented sheet metal prototyping to design custom kitchen equipment, resulting in improved ergonomics and reduced risk of injuries for staff.
These case studies demonstrate the valuable role sheet metal prototyping plays in improving efficiency, hygiene, and overall performance in the food processing industry.
Conclusion
Sheet metal prototyping has become an indispensable tool in the food processing industry. Its versatility, cost-effectiveness, and ability to meet strict hygiene and compliance standards make it a valuable asset for developing and optimizing equipment, components, and processes. As the food processing industry continues to evolve, sheet metal prototyping will undoubtedly remain a key player in driving innovation, efficiency, and safety within the industry.